Viscosity, a measure of a fluid’s resistance to flow, is a critical property in various industries, including food, pharmaceuticals, cosmetics, and oil and gas. Rotational viscometers are a versatile tool for measuring the viscosity of fluids. They work by applying rotational force to a fluid sample and analyzing the resulting torque to determine its resistance to flow. But they have different types, and each type is tailored to different fluid properties, shear conditions, and testing requirements. So selecting the correct type of rotational viscometer is crucial for the precise results. We are here to discuss the components, types, and selection criteria for rotational viscometers to help you identify the best choice for your testing needs.
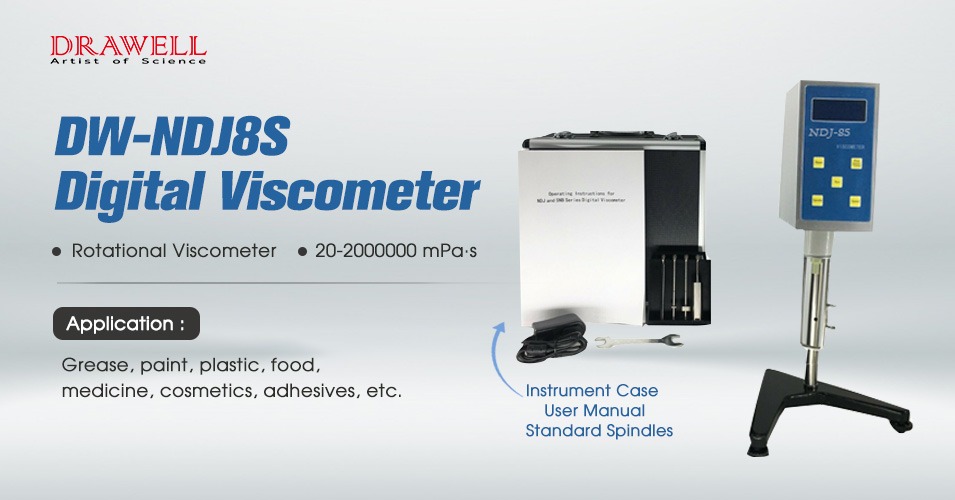
Key Components of a Rotational Viscometer
To understand how rotational viscometers work and how they differ, it’s essential to know their core components. Each component plays a role in measuring the viscosity accurately and consistently.
- Spindle:
The spindle is the rotating component that comes into direct contact with the fluid. Different spindle geometries are available to accommodate various viscosity ranges and fluid types. Common spindle types include:
- Cone and Plate: This configuration offers precise measurements, especially for non-Newtonian fluids. The cone-shaped spindle rotates very close to a flat plate, minimizing edge effects.
- Cylinder (Bob and Cup): A cylindrical spindle rotates inside a cylindrical cup. This configuration is suitable for a wide range of viscosities, from low to high.
- Vane: A flat, paddle-shaped spindle is used for measuring the viscosity of highly viscous materials, such as pastes and gels.
- Rotating Spindle: This type uses various spindle shapes (e.g., T-bar, paddle, cylinder) to accommodate different viscosity ranges.
- Motor:
The motor drives the spindle at a specific speed, which is crucial for accurate viscosity measurements. The motor’s power and speed range should be appropriate for the desired measurement range.
- Torque Sensor:
The torque sensor measures the resistance to rotation exerted by the fluid on the spindle. This torque measurement, along with the spindle geometry and rotational speed, is used to calculate viscosity.
- Temperature Control:
Temperature significantly influences viscosity. Therefore, precise temperature control is essential for accurate measurements. Many rotational viscometers include temperature control systems to maintain a constant temperature during testing.
The components of a rotational viscometer work together to capture accurate viscosity measurements.
Types of Rotational Viscometers
Rotational viscometers, used to measure the viscosity of liquids by analyzing the torque needed to rotate an object in the fluid, are classified based on various characteristics, such as the type of measurement system, design, and applications. Here are the common types:
1. Based on Measurement System
- Brookfield Viscometer: Measures viscosity by rotating a spindle in the fluid, widely used for low- to medium-viscosity materials.
- Cone and Plate Viscometer: Utilizes a cone and plate geometry for high-shear rate measurements, ideal for low-viscosity samples.
- Coaxial Cylinder (or Couette) Viscometer: Consists of two concentric cylinders; one rotates while the other is stationary, suitable for a wide range of viscosities and accurate shear rate control.
2. Based on Operating Mechanism
- Controlled-Rate (CR) Viscometer: Controls the rotational speed to maintain a constant shear rate, allowing viscosity measurement under specific shear conditions.
- Controlled-Stress (CS) Viscometer: Controls the applied stress or torque, measuring how the fluid responds, useful for non-Newtonian fluids where viscosity changes with shear rate.
3. Based on Viscosity Range
- Low-Viscosity Rotational Viscometers: Specialized for measuring thin, watery solutions with low resistance to rotation.
- High-Viscosity Rotational Viscometers: Designed for thick, viscous samples, like gels or pastes, where higher torque is needed.
4. Based on Application and Industry
- Laboratory Viscometers: General-purpose viscometers for standard lab use, typically used in R&D, quality control, or product development.
- Process Viscometers: Inline viscometers designed for real-time viscosity monitoring in manufacturing processes, helping ensure consistency in products like paints, coatings, and adhesives.
- Portable Viscometers: Lightweight and easy-to-use viscometers for on-site measurements, convenient for field testing and industrial inspections.
Each classification caters to specific sample characteristics and industry needs, so selecting the appropriate viscometer type depends on the viscosity range, shear behavior, and testing environment.
Here are the comparison table of the common types of rotational viscometer:
Type of Viscometer | Pros | Cons | Typical Applications |
Brookfield Viscometer | Versatile, suitable for lowto medium-viscosity fluids | Limited precision for high-shear applications | Quality control in food, cosmetics, and general lab testing |
Affordable and user-friendly | Less suitable for non-Newtonian fluids | ||
Cone and Plate Viscometer | Precise shear control | Limited to low-viscosity fluids | Low-viscosity fluids like inks, coatings, and emulsions |
Ideal for low-viscosity samples | Can be expensive | ||
High sensitivity | |||
Coaxial Cylinder Viscometer | Suitable for a wide range of viscosities | Bulkier design | Testing non-Newtonian fluids, such as paints, slurries, gels |
Excellent for non-Newtonian fluids | Requires more sample volume | ||
Controlled-Rate (CR) Viscometer | Consistent shear rate control | Limited to fixed shear rates | Research on fluids requiring steady shear rate measurements |
Precise and reliable for specific shear conditions | Often more costly | ||
Controlled-Stress (CS) Viscometer | Ideal for non-Newtonian fluids | Generally more expensive | Testing gels, biological fluids, and other stress-sensitive fluids |
Suitable for materials with stress-sensitive viscosity | Complex to operate | ||
Portable Viscometer | Lightweight and easy for on-site use | Lower precision than lab-based models | Field inspections and on-site viscosity measurements |
Quick measurements | Limited for high-viscosity fluids | ||
Process Viscometer | Designed for continuous, inline monitoring | Limited versatility outside of specific applications | Real-time viscosity monitoring in manufacturing, such as paints, coatings, and adhesives |
Durable for industrial environments | Typically more costly |
Hope this table can help you choose the right rotational viscometer that fits your testing needs. You can also refer to the following suggestions.
How to Choose the Right Type of Rotational Viscometer
Selecting the correct rotational viscometer depends on your specific testing needs, including the fluid properties, required accuracy, and testing environment.
- Consider the Sample Viscosity Range: Different viscometers are suitable for various viscosity ranges. Brookfield viscometers, for example, are ideal for low- to medium-viscosity fluids, while coaxial cylinder viscometers are better for higher viscosities.
- Determine the Shear Conditions Required: Some fluids, especially non-Newtonian, behave differently at various shear rates. If precise shear control is essential, a cone and plate or coaxial cylinder viscometer would be a good choice. For fluids needing stress-controlled conditions, a controlled-stress viscometer is appropriate.
- Evaluate Temperature Sensitivity: Temperature can impact viscosity significantly, so if your fluid is temperature-sensitive, choose a viscometer with temperature control capabilities or compatibility with external temperature control systems.
- Choose Based on Application Environment: Laboratory testing and industrial process monitoring require different viscometer types. Portable viscometers are excellent for field testing, while process viscometers are designed for continuous, inline monitoring in industrial settings.
- Consider the Budget and Ease of Use: Laboratory viscometers vary in cost and complexity. Controlled-stress viscometers are generally more expensive due to their advanced control, while Brookfield viscometers offer a cost-effective solution for basic viscosity measurements.
By considering factors like viscosity range, shear requirements, temperature sensitivity, and budget, you can choose the best type of rotational viscometer to fit your specific testing needs, ensuring accurate and reliable measurements for your fluid applications. Feel free to contact us if you need any help. We have professional team to serve your needs.