Refrigerated centrifuges facilitate the separation of mixtures based on density while maintaining low temperatures to preserve the integrity of temperature-sensitive samples. The precise control and stability of temperature within these centrifuges are crucial for ensuring the accuracy and reproducibility of experimental results. This article explores the importance of temperature stability and control in refrigerated centrifuges, the challenges involved, and the technologies that address these challenges.
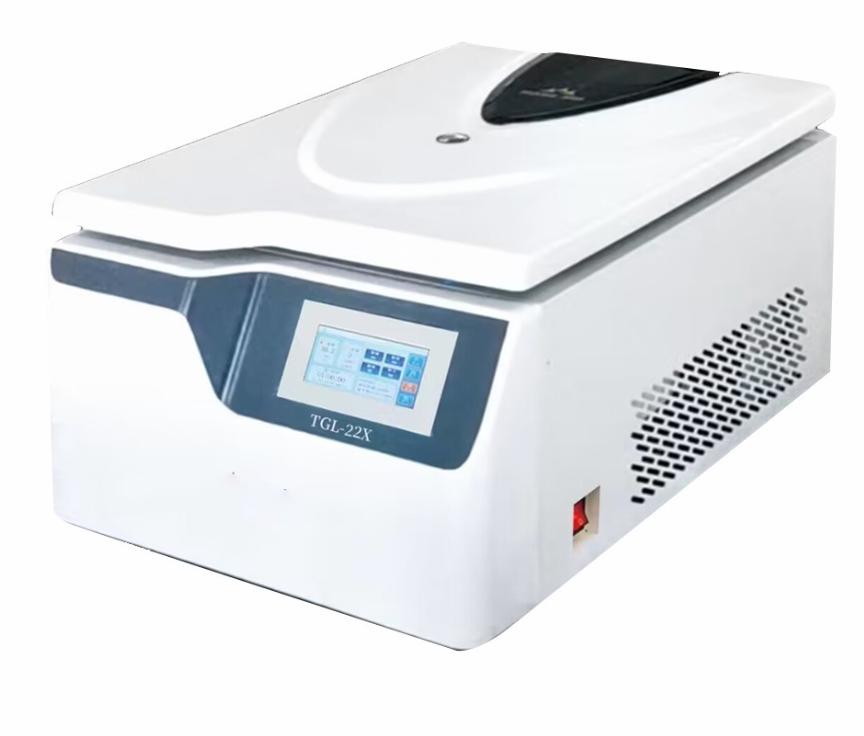
Importance of Temperature Stability in Refrigerated Centrifuges
Aspect | Importance |
Sample Integrity | Prevention of Degradation: Maintains the biological activity and structure of sensitive samples (proteins, nucleic acids, enzymes). |
Avoidance of Sample Loss: Prevents thermal denaturation or breakdown of cellular structures, ensuring sample preservation. | |
Reproducibility of Results | Consistent Conditions: Ensures that experimental conditions are consistent across different runs, leading to reliable and comparable results. |
Minimization of Variables: Reduces the influence of temperature fluctuations as a variable, ensuring observed changes are due to experimental conditions. | |
Accurate Separation | Optimal Centrifugation: Ensures that samples are separated effectively based on their density, without the interference of temperature-induced anomalies. |
Quality Control | Regulatory Compliance: Meets strict regulatory standards and guidelines for processes involving temperature-sensitive materials. |
Product Integrity: Ensures the quality and efficacy of products, particularly in pharmaceuticals and biotechnology. | |
Extended Equipment Lifespan | Reduced Wear and Tear: Minimizes the stress on refrigeration systems and mechanical components, leading to longer equipment life. |
Operational Efficiency | Reduced Downtime: Ensures reliable operation, minimizing the risk of equipment failure and associated downtime. |
Data Integrity | Accurate Records: Maintains the integrity of experimental data by ensuring that temperature is a controlled and consistent parameter. |
Cost Efficiency | Minimized Sample Waste: Reduces the loss of valuable samples, leading to cost savings in reagents and materials. |
Safety | Safe Handling: Ensures safe handling and processing of biohazardous and temperature-sensitive materials. |
Challenges in Temperature Control for Refrigerated Centrifuges
1. Heat Generation During Operation
- Centrifugal Force: High-speed centrifugation generates significant heat due to friction and air resistance. This heat can increase the internal temperature, which may compromise the integrity of temperature-sensitive samples.
- Mechanical Components: Motors and other mechanical components within the centrifuge also produce heat. This internal heat generation poses a challenge for maintaining a stable, low temperature, especially during extended runs.
2. Environmental Factors
- Ambient Temperature: The temperature of the environment where the centrifuge operates can significantly impact its internal temperature stability. Fluctuations in room temperature, particularly in non-climate-controlled environments, can strain the centrifuge’s refrigeration system.
- Humidity: High humidity levels can lead to condensation inside the centrifuge. Condensation not only affects temperature control but can also interfere with the mechanical and electronic components of the centrifuge.
3. Rapid Temperature Changes
- Speed of Cooling: Quickly lowering the temperature to the desired set point can be challenging, especially after the centrifuge has been running at high speeds. Rapid temperature changes require efficient cooling systems capable of handling sudden thermal loads.
- Uniform Cooling: Ensuring uniform cooling throughout the centrifuge chamber is critical. Inconsistent temperature distribution can result in uneven cooling of samples, affecting their stability and the accuracy of experimental results.
4. Calibration and Maintenance
- Sensor Accuracy: Temperature sensors must be highly accurate and regularly calibrated to ensure reliable readings. Sensor drift over time can lead to incorrect temperature settings, potentially compromising sample integrity.
- System Maintenance: The refrigeration system requires regular maintenance to function optimally. Issues such as refrigerant leaks, compressor wear, or blocked ventilation can impair temperature control, necessitating routine inspections and servicing.
5. Energy Consumption
- High Energy Demand: Maintaining low temperatures in a high-speed refrigerated centrifuge requires substantial energy, particularly for powerful compressor-based systems. Balancing energy efficiency with effective temperature control is a constant challenge.
- Operational Costs: The high energy consumption associated with maintaining precise temperature control translates to increased operational costs, which can be a concern for laboratories with budget constraints.
6. Load Variability
- Sample Volume and Type: The type and volume of samples can affect the centrifuge’s ability to maintain stable temperatures. Large volumes or samples with high thermal mass may require more intensive cooling efforts.
- Run Duration: Extended centrifugation runs can lead to temperature drift, as the refrigeration system must continuously counteract the heat generated by the centrifuge’s operation.
Addressing the Challenges in Temperature Control for Refrigerated Centrifuges
To overcome these challenges and achieve and maintain the required temperature stability, several strategies and advanced technologies are employed.
1. Advanced Refrigeration Systems
Compressor-Based Systems
- Description: Utilizes powerful compressors to rapidly cool the centrifuge chamber.
- Benefits: Efficiently brings the internal temperature down to the desired set point and maintains it consistently, even during high-speed operations.
- Applications: Commonly used in high-capacity centrifuges requiring quick and reliable cooling.
Thermoelectric (Peltier) Cooling
- Description: Uses the Peltier effect to achieve precise temperature control by creating a heat flux between the junctions of two different types of materials.
- Benefits: Provides rapid temperature adjustments with high precision and is energy efficient.
- Applications: Suitable for smaller, benchtop centrifuges where precise temperature control is needed without the noise and maintenance of compressor systems.
2. Real-Time Temperature Monitoring and Feedback
Temperature Sensors
- Description: Sensors placed inside the centrifuge chamber to continuously monitor temperature.
- Benefits: Provides real-time data on the internal temperature, ensuring any deviations are quickly detected and corrected.
- Applications: Essential in all refrigerated centrifuges for maintaining precise temperature control.
Automated Feedback Control Systems
- Description: Systems that automatically adjust the refrigeration cycle based on real-time temperature data from sensors.
- Benefits: Ensures precise and consistent temperature control by dynamically responding to any changes.
- Applications: Used in advanced centrifuges to maintain stable temperature conditions during varying operational loads.
3. Insulation and Sealing
High-Quality Insulation
- Description: Utilizes effective insulation materials to reduce heat exchange between the centrifuge chamber and the external environment.
- Benefits: Helps maintain a stable internal temperature by minimizing external thermal influence.
- Applications: Integral to all refrigerated centrifuges, particularly those operating in fluctuating ambient conditions.
Sealed Chambers
- Description: Design features that ensure tight sealing of the centrifuge chamber to prevent air exchange.
- Benefits: Reduces the impact of external temperature and humidity fluctuations, contributing to consistent internal conditions.
- Applications: Critical for maintaining temperature stability in high-performance centrifuges.
4. Programmable Temperature Settings
User-Defined Protocols
- Description: Allows users to program specific temperature profiles for different stages of the centrifugation process.
- Benefits: Provides flexibility to optimize conditions for various sample types and experimental protocols.
- Applications: Used in sophisticated centrifuges to cater to diverse laboratory needs and sample requirements.
5. IoT and Connectivity
Remote Monitoring and Control
- Description: Incorporates Internet of Things (IoT) technology to enable remote monitoring and control of centrifuge temperature settings.
- Benefits: Allows for greater flexibility and oversight, ensuring sample integrity even when researchers are not physically present.
- Applications: Particularly useful in large laboratories or facilities where centralized monitoring of multiple centrifuges is needed.
6. Enhanced Energy Efficiency
Energy-Efficient Components
- Description: Utilizes advanced refrigeration components designed for lower energy consumption.
- Benefits: Reduces operational costs and environmental impact while maintaining effective cooling.
- Applications: Applied in modern centrifuge designs to balance performance with sustainability.
7. Advanced User Interfaces
Intuitive Controls
- Description: Features user-friendly interfaces with touchscreen controls and advanced software.
- Benefits: Simplifies the process of setting and monitoring temperature conditions, reducing the likelihood of user error.
- Applications: Found in the latest centrifuge models to enhance usability and operator efficiency.
Conclusion
Temperature stability and control are vital for the effective operation of refrigerated centrifuges. Through advanced refrigeration systems, real-time monitoring, and precise control mechanisms, modern centrifuges ensure the integrity and reproducibility of experimental results.