Freeze drying, or lyophilization, is a crucial process in the pharmaceutical, food, and biotechnology industries, used to preserve perishable materials by removing water content. A key component of a freeze dryer is the ice condenser, an essential part of the machinery that ensures the efficiency and effectiveness of the lyophilization process. This article delves into the role, function, and importance of the ice condenser in freeze dryers.
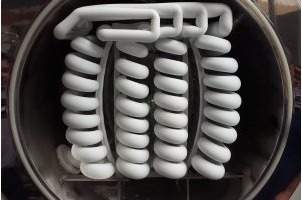
Understanding the Freeze Drying Process
Before exploring the ice condenser’s role, it’s important to understand the freeze drying process. This chart outlines the key stages of the freeze-drying process, highlighting the main actions and objectives at each step.
Stage | Description |
1. Pretreatment | Preparation of the product (e.g., cleaning, slicing, blanching).Optional: Adding preservatives or treatments to enhance quality. |
2. Freezing | Lowering the product temperature below its triple point.Ensures that sublimation (solid to gas) can occur.Rapid freezing helps form small ice crystals, preserving cell structure. |
3. Primary Drying (Sublimation) | Lowering the pressure and adding heat to the product.Ice converts directly to vapor without passing through the liquid phase.Approximately 95% of water is removed during this stage. |
4. Secondary Drying (Desorption) | Further reduction of pressure and temperature.Removes unfrozen water molecules bound to the product.Ensures final moisture content is typically 1-4%. |
5. Packaging | Sealing the dried product in airtight containers to prevent moisture reabsorption.Often done under vacuum or in an inert gas atmosphere. |
The ice condenser becomes particularly vital during the primary drying stage, where it captures and condenses the water vapor generated from sublimation.
Role and Function of the Ice Condenser
The ice condenser, often referred to as a cold trap, serves to capture the sublimated water vapor from the product chamber. Here’s a detailed look at its primary functions.
1. Vapor Capture
As ice sublimates from the product, it turns into water vapor. The ice condenser, maintained at very low temperatures (typically between -40°C to -80°C), attracts and captures this vapor, condensing it back into ice.
2. Maintaining Vacuum
By removing water vapor from the product chamber, the ice condenser helps maintain the low-pressure conditions necessary for sublimation. This stable vacuum environment is crucial for the efficiency of the freeze drying process.
3. Preventing Recondensation
Effective vapor capture by the ice condenser prevents water vapor from re-entering and re-condensing on the product, ensuring consistent drying.
Design and Operational Considerations of Ice Condenser in Freeze Dryers
Proper design and operational strategies are essential for ensuring optimal performance.
Design Considerations
1. Surface Area
- Importance: A larger surface area provides more space for water vapor to condense, increasing the efficiency of the process.
- Implementation: Use designs that maximize the exposed surface area, such as coiled or finned structures, to enhance condensation efficiency.
2. Material Selection
- Importance: Materials used in the construction of the condenser should have high thermal conductivity and resistance to corrosion.
- Implementation: Stainless steel is commonly used due to its durability, thermal properties, and resistance to corrosion.
3. Condenser Capacity
- Importance: The condenser must be capable of handling the expected load of water vapor without becoming overwhelmed.
- Implementation: Design the condenser to match the capacity requirements of the freeze dryer, taking into account the volume of the product being dried and the amount of water it contains.
4. Insulation
- Importance: Proper insulation minimizes heat gain, ensuring that the condenser remains at the required low temperatures.
- Implementation: Use advanced insulation materials and techniques to reduce thermal losses and improve energy efficiency.
Operational Considerations
1. Defrosting Cycles
- Importance: Ice buildup on the condenser can reduce its efficiency, so regular defrosting is necessary to maintain optimal performance.
- Implementation: Schedule regular defrosting cycles and incorporate automated defrosting systems to ensure consistent operation without manual intervention.
2. Monitoring and Control
- Importance: Continuous monitoring of the condenser’s performance helps in identifying and addressing issues promptly.
- Implementation: Use sensors and automated control systems to monitor temperature, pressure, and ice buildup. Implement alarms and automatic adjustments to maintain optimal conditions.
3. Load Management
- Importance: Properly managing the load ensures the condenser operates within its capacity, preventing overload and potential failure.
- Implementation: Plan and control the amount of product being freeze-dried to match the condenser’s capacity. Avoid overloading the system to maintain efficiency and prevent damage.
Challenges of Ice Condensers in Freeze Dryers
1. Ice Buildup
- Issue: Continuous condensation of water vapor leads to ice accumulation on the condenser surface, reducing its efficiency.
- Impact: Excessive ice buildup can block the condenser, decrease the rate of water vapor capture, and impair the vacuum conditions necessary for effective freeze drying.
- Solution: Implement regular defrost cycles to remove the accumulated ice and restore the condenser’s efficiency.
2. Energy Consumption
- Issue: Maintaining the low temperatures required for effective condensation consumes significant energy.
- Impact: High energy usage increases operational costs and can strain the cooling system.
- Solution: Employ energy-efficient refrigeration systems, use advanced insulation techniques, and explore heat recovery options to minimize energy consumption.
3. Mechanical Wear and Tear
- Issue: Continuous operation and extreme temperature conditions can cause wear and tear on mechanical components such as compressors, seals, and vacuum pumps.
- Impact: Mechanical failure can lead to system downtime, reduced efficiency, and increased maintenance costs.
- Solution: Regularly inspect and service mechanical components, replace worn parts promptly, and maintain a supply of critical spare parts to minimize downtime.
4. Vacuum Leaks
- Issue: Leaks in the vacuum system can compromise the low-pressure environment required for sublimation.
- Impact: Vacuum leaks reduce the efficiency of the drying process and can lead to incomplete drying or product spoilage.
- Solution: Regularly check for and repair any leaks in the vacuum system, and ensure that seals and gaskets are in good condition.
5. Temperature Control
- Issue: Maintaining consistent low temperatures is challenging, especially during long drying cycles.
- Impact: Temperature fluctuations can reduce the condenser’s ability to capture water vapor effectively.
- Solution: Use precise temperature control systems, regularly calibrate sensors, and monitor temperature conditions closely.
6. Scaling and Contamination
- Issue: Deposits from sublimated materials can build up on the condenser, reducing its efficiency.
- Impact: Scaling and contamination can impair heat transfer and reduce the effectiveness of the condenser.
- Solution: Implement regular cleaning protocols to remove any deposits or contaminants from the condenser surfaces.
Maintenance Considerations of Ice Condensers in Freeze Dryers
1. Regular Defrosting
- Schedule routine defrost cycles to remove ice buildup and maintain the condenser’s efficiency.
- Use automated defrost systems to ensure consistent and timely defrosting without manual intervention.
2. Inspection and Servicing
- Conduct regular inspections of the condenser and associated components, including compressors, vacuum pumps, and seals.
- Replace worn or damaged parts promptly to prevent system failures.
3. Temperature Monitoring
- Continuously monitor the temperature of the condenser using sensors and automated control systems.
- Ensure that the refrigeration system is functioning correctly and maintaining the required low temperatures.
4. Vacuum System Maintenance
- Regularly check for leaks in the vacuum system and repair any detected issues.
- Maintain seals and gaskets in good condition to ensure a stable vacuum environment.
5. Energy Efficiency Measures
- Use energy-efficient refrigeration units and advanced insulation to reduce energy consumption.
- Explore heat recovery options to reuse waste heat and improve overall energy efficiency.
6. Cleaning Protocols
- Implement regular cleaning schedules to remove any scaling or contamination from the condenser surfaces.
- Use appropriate cleaning agents and methods to ensure the condenser remains free of deposits and operates at peak efficiency.
7. Spare Parts Inventory
- Maintain a stock of critical spare parts to minimize downtime in case of component failure.
- Ensure that parts such as compressors, vacuum pumps, and seals are readily available for quick replacement.
Innovations for Ice Condenser Technology in Freeze Dryers
Innovations in ice condenser technology aim to enhance efficiency, reduce energy consumption, and improve reliability.
1. Advanced Cooling Technologies
Cryogenic Cooling
Utilizing cryogenic fluids such as liquid nitrogen can achieve significantly lower temperatures more efficiently than conventional methods. This enables faster and more efficient vapor capture, reducing overall drying time.
Thermoelectric Cooling
Solid-state thermoelectric coolers offer precise temperature control and minimal mechanical wear. These devices operate using the Peltier effect, which can provide cooling without the need for traditional refrigeration systems.
2. Enhanced Materials and Coatings
High Thermal Conductivity Materials
The development of materials with superior thermal properties, such as advanced alloys or composites, improves heat transfer efficiency. These materials ensure rapid cooling and effective condensation of water vapor.
Anti-fouling and Anti-icing Coatings
Innovative coatings prevent ice buildup and scaling, maintaining the condenser’s efficiency and reducing maintenance requirements. Nanotechnology-based coatings, in particular, offer high performance in preventing ice adhesion.
3. Optimized Design Structures
Increased Surface Area Designs
New geometries that maximize surface area, such as finned or honeycomb structures, enhance the condenser’s capacity to capture water vapor. This design optimization leads to more efficient drying cycles.
Modular Condensers
Modular designs allow for scalability and easy maintenance. These condensers can be tailored to specific capacity requirements and enable straightforward upgrades or repairs without extensive downtime.
4. Smart Monitoring and Control Systems
IoT Integration
The Internet of Things (IoT) enables real-time monitoring and control of condenser performance. IoT sensors provide continuous data on temperature, pressure, and ice buildup, facilitating proactive adjustments.
AI and Machine Learning
Artificial intelligence (AI) and machine learning algorithms analyze operational data to optimize performance, predict maintenance needs, and enhance energy efficiency. These technologies enable automated and adaptive control systems that improve overall system reliability.
5. Energy Efficiency Improvements
Variable Speed Compressors
Variable speed compressors adjust their cooling power based on real-time demand, reducing energy consumption and improving efficiency. This adaptability ensures optimal performance under varying load conditions.
Heat Recovery Systems
Heat recovery systems capture waste heat from the condenser and repurpose it within the freeze drying process, such as preheating the drying chamber. This not only improves energy efficiency but also reduces operational costs.
6. Automated Maintenance Systems
Self-cleaning Mechanisms
Automated systems that periodically remove ice and contaminants without manual intervention help maintain condenser efficiency and reduce downtime. These self-cleaning mechanisms ensure consistent performance.
Predictive Maintenance
Advanced sensors and data analytics predict when maintenance is required, allowing for scheduled servicing that minimizes unexpected breakdowns. Predictive maintenance ensures continuous operation and prolongs equipment lifespan.
7. Nanotechnology Applications
Nano-coatings
Ultra-thin nano-coatings enhance the thermal conductivity and anti-icing properties of condenser surfaces. These coatings reduce ice buildup and improve the efficiency of water vapor condensation.
Nanomaterials
Incorporating nanomaterials with exceptional thermal properties can significantly improve the performance and durability of condensers. Nanomaterials offer enhanced heat transfer and resistance to wear and corrosion.
8. Hybrid Systems
Combination Cooling Technologies
Hybrid systems that combine different cooling methods, such as cryogenic and thermoelectric cooling, leverage the advantages of each technology. This approach offers more flexible and efficient operation tailored to specific drying needs.
Integrated Preservation Methods
Integrating freeze drying with other preservation methods within a single system can enhance overall efficiency and capabilities. For example, combining vacuum drying and freeze drying can optimize the preservation of sensitive materials.
Conclusion
The ice condenser is an indispensable element of freeze dryers, playing a crucial role in the lyophilization process. Its ability to capture and condense water vapor ensures the integrity and quality of the dried product. As technology advances, the efficiency and effectiveness of ice condensers will continue to improve, driving further innovations in freeze drying applications.